When medical or pharma product launch failure happens the field, everyone suffers—not just the patient, but also the manufacturer and its employees, investors, suppliers, and even competitors. No one wants a product failure, least of all the company liable for its safety.
Faced with a crisis, the manufacturer has three priorities:
- Protect patients;
- Resolve the problem as quickly as possible
- Prevent the problem from recurring.
Any number of product failures can threaten a huge loss of value, above and beyond liability, to the manufacturer. If investors lose confidence and share price falls, enterprise value is destroyed. Then, as the company dedicates resources to resolving the problem, their other jobs—such as new product development—don’t get done (or, at best, don’t get done as quickly).
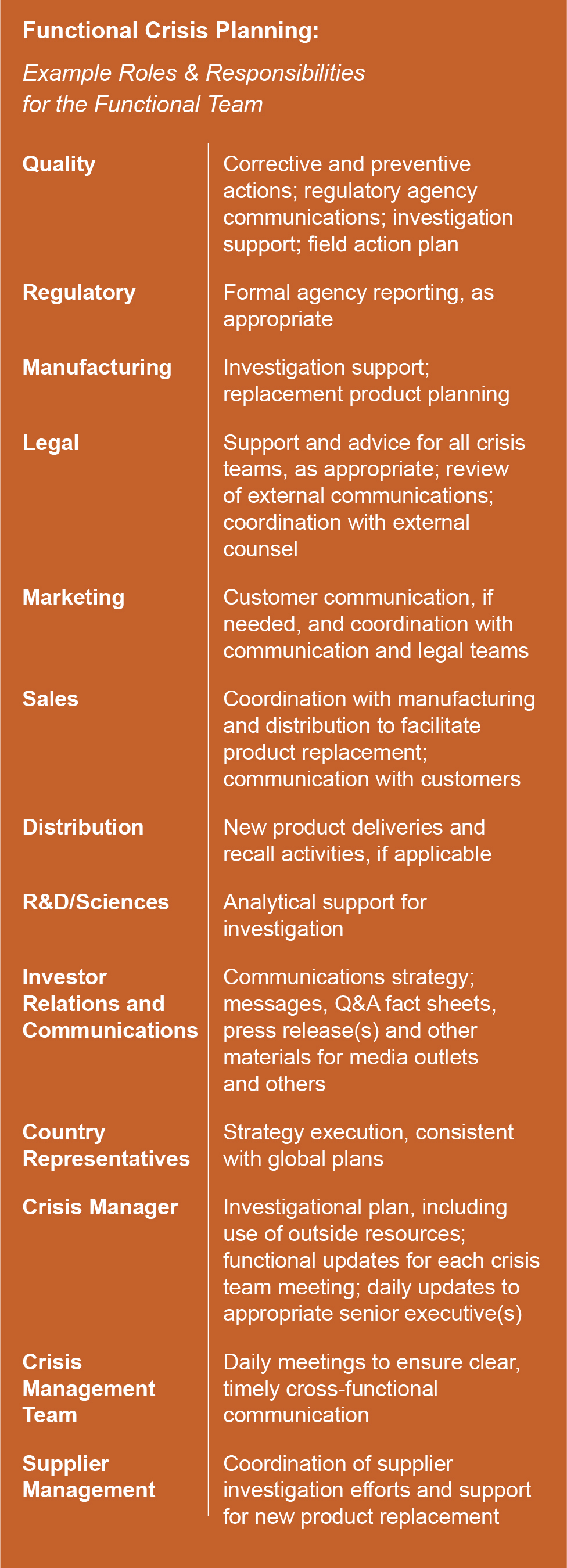
Pharmaceutical Innovation
Since innovation is the beating heart of the medical products and pharmaceutical industries, any delay of a new product launch can cost a manufacturer millions; in these industries, time really is money. All the more reason that speed is so important in fixing any product problem.
Yet, many—maybe most—companies are not really prepared for product failures because they lack a crisis playbook. Without a scenario-based guide, they begin and often conduct an investigation in a somewhat helter-skelter fashion, wasting valuable time figuring out what to do first, and next, and after that.
Crisis Management
The optimal time to answer those “what to do” questions is before a crisis, not in the middle of one. In our work, helping companies investigate and resolve product failures, Regulatory Compliance Associates® and The Science Cooperative have gained the following insights about what works (and what doesn’t) in managing a product crisis.
Pharma Product Launch Problems
A problem is identified as serious when field events reach some specified tipping point that indicates a trend beyond isolated incidences. At that time, the company’s leadership team has to make a few decisions: Should an official notice be released? Should the product be recalled? If yes, which markets? Should production of the product be stopped? In multiple or select plants?
Prompt action generally contributes to good will and positive publicity. The challenge at this stage is a deficit of facts since the forensic investigation itself hasn’t started. In putting together a crisis playbook, a company should begin with guidelines and policies to direct the first responders in evaluating the size of the threat and the appropriateness of various options for response depending on the apparent scope and severity of the problem.
Supply Chain
For example, if a product is one component in an assembly, perhaps the best response is for multiple supply chain owners to work together to find the optimal fix for the problem. The “point man” for making that happen could be decided in advance.
Of course, a crisis playbook would also help business leaders evaluate the cost of alternative responses. Scenario-based planning provides a context for weighing alternatives and options. Above all else, the first responders would want to stop patient harm. Every manufacturer we have worked with has agreed: protecting the safety of the patient population comes first.
Pharma Product Launch Teams
After the first responders have reviewed the situation and decided there is cause for escalation, it is time to identify a crisis manager, an investigation leader and the functional forensic team(s). In our experience, an attorney or senior executive with strong project management skills is a good choice for crisis manager. Also, each team needs at least one member with strong organizational skills.
The crisis playbook should cover roles and responsibilities—including potential action checklists—for multiple functional teams. It is feasible that a crisis might require teams in R&D, sciences, manufacturing, distribution, supply chain, human resources, legal, regulatory, quality, environmental, sales/marketing, and communications, as well as subteams for representatives from affected countries and from government affairs.
Crisis Playbook
What expertise would each team require? What would be each team’s scope and focus? Most important, how should the teams interact, coordinate activities, and measure progress toward milestones and a final resolution? A crisis playbook should provide answers, which would vary case-by-case. (See the sidebar, “Functional Crisis Planning: Roles and Responsibilities for the Crisis Team”). The crisis playbook should cover roles and responsibilities – including potential action checklists – for multiple functional teams.
Good project management skills are fundamental to managing the investigation process effectively and efficiently. Although the teams are all working on the same problem, each has its own agenda and requires its own plan and milestones. Role-based accountability for project and team-specific organization, documentation, schedules, data management, and reporting can be decided well in advance of a crisis.
In our experience, it is a best practice for the leaders of the crisis management team to meet daily and assure clear, timely, cross-functional communication, as well as to agree on next steps.
Pharma Product Launch: Crisis Roadmap
If valuable resources are taken away or distracted from their jobs to any significant degree, real and measurable enterprise value is destroyed. While leaders and experts from each affected corporate function play a vital role in an investigation, it is a smart business strategy to bring in specialists to support the effort with their expertise and experience.
FDA Investigation
In addition to minimizing damage to the company’s value and brand, the quick building up of expertise also speeds up the forensic process itself. One of our clients asked both the FDA and the notified body for its European markets to participate in an investigation. As a result, the company tripled its lab capacity and bolstered its credibility with shareholders and the marketplace at large.
Independent consultants can add muscle to an investigation, while buttressing investor confidence. As an added benefit, they can often give employees the freedom to speak without repercussion because they’re beyond the “politics” of the enterprise. Also, outside resources with the right knowledge and “know how” will be well-versed in Corrective and Preventive Action (CAPA) processes and can use this expertise to streamline and speed up the investigation.
Pharma Product Launch New Direction
Each team needs a directed course of action based on scenario planning. Given a set of regulatory variables that would vary by product and case—including (but not limited to) the severity of the crisis, geography, financial liability, and the possibility of substitute products—what steps should each team take to contribute to the problem identification, resolution, and ongoing prevention?
The steps required of each team can be captured in “punch lists” to minimize redundancy and duplication of effort. Then, it is relatively easy to assign responsibility for each item on the list. If the product is used in more than one country or region, the work of the corporate teams needs to be mirrored by local teams. And everyone’s findings need to roll up to the top.
Deviations
Perhaps one of the most critical points in the investigation roadmap—and the one that is most often missing—is a “stop” point. The longer an investigation goes on, the more enterprise value it can destroy. In the beginning, it’s important to decide: when is the problem solved? Is it when the contaminant is found? When the deviations in the factory or the supply chain process is fixed? Or when the product is reintroduced to the market?
Among these inquiries is another with implications for continuous improvement: why didn’t the QA processes in place (for design, manufacturing, and other functions) detect the potential failure? Scope control is a fundamental component of good project management. In most cases, there is no need to parse the product failures problem beyond a practical solution.
Crisis Checklist
The crisis playbook should include prototype action plans, checklists, work streams, decision processes, schedules, milestones, resource requirements, budgets, and documentation (see the sidebar, “Steps for Post-Crisis Resolution”).
Pharma Product Launch Communication
From day one, the crisis manager needs to share information about commitments, expectations, and progress. Communication—internally with employees and externally with investors, supply chain partners, regulatory agencies, the public, and sometimes competitors—is critically important.
Crisis Communication
The overall process needs a “point person” for communication, as does each team, whether at the corporate or facility level. The role of each communication channel—including press releases, internal newsletters or briefs, media contacts, video, and letters to shareholders and the investment community—can be planned well in advance: a crisis playbook can take chaos out of the process and enable the company to put its best foot forward.
In communication, the current best practice is a dedicated portal, a single source for real-time updates on the investigation, typically accessible through the company’s website. The old proverb “a stitch in time saves nine” captures the value of a crisis playbook: being prepared will save time and money down the road.
Key Steps in Crisis Management
Most importantly, fewer product failures could literally save lives. By being mindful of the components of effective and efficient crisis management—building up and deploying expert resources; coordinating and integrating parallel work streams; following and documenting rationalized processes—a company’s leadership can be confident in its preparedness to handle a product failure to the satisfaction of everyone’s best interests.
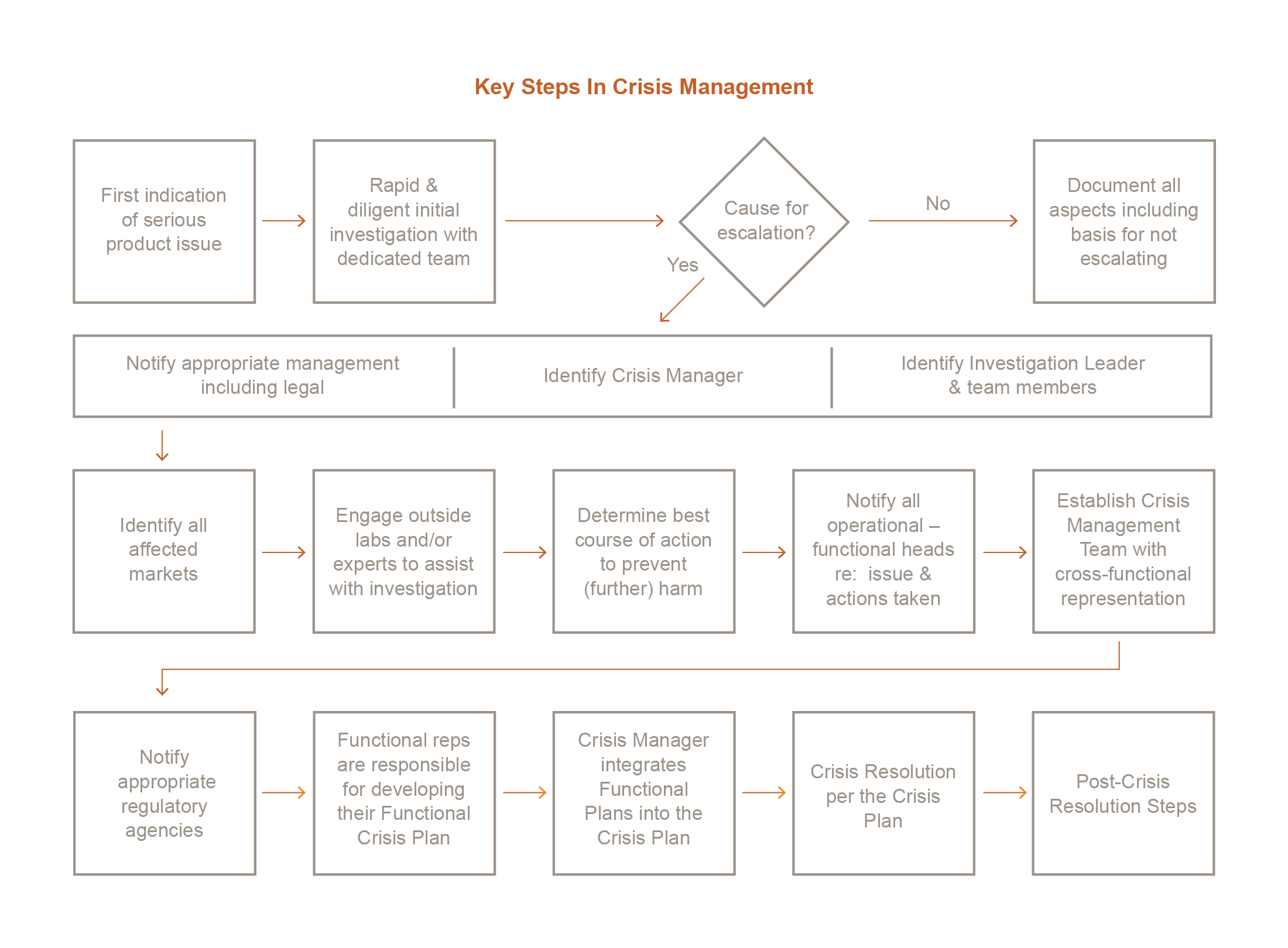
Regulatory Compliance Associates (RCA) has helped thousands of pharmaceutical companies meet regulatory, compliance, quality assurance, and remediation challenges. With more than 20 years of experience with FDA, Health Canada, EU and global regulatory agencies worldwide, Regulatory Compliance Associates® offers leading pharmaceutical consultants. We’re one of the few pharma consulting companies that can help you navigate the challenges associated with industry regulations.
Our pharmaceutical consulting firm includes over 500 seasoned FDA, Health Canada & EU compliance consultants and regulatory affairs experts who understand industry complexities. It’s a pharma consultancy founded by regulatory compliance executives from the pharmaceutical industry. Every pharmaceutical industry consultant on the Regulatory Compliance Associates team knows the unique inner workings of the regulatory process.
Client Solutions
Whether you’re in the product planning, development or pharmaceutical lifecycle management stage or need a remediation strategy for a compliance crisis, Regulatory Compliance Associates will guide you through every pharmaceutical consulting step of the regulatory process and create a customized approach depending on your product and your pharma company’s individual needs. Our regulatory compliance clients include:
- Companies new to FDA, Health Canada or EU regulations and regulatory compliance
- Start-up organizations with novel submissions to 510(k) submissions from multi-national corporations
- Investment firms seeking private equity due diligence for pre-acquisition and post-deal research
- Law firms seeking pharmaceutical consulting firm expertise in the remediation of warning letters, consent decrees, 483’s or import bans
Regulatory affairs is Regulatory Compliance Associates backbone. We exceed other pharma consulting companies with industry experts experienced in complexities of the pharmaceutical and biopharmaceutical industries. Our pharma consulting expertise spans all facets and levels of Regulatory Affairs, from Regulatory Support for New Products to Life Cycle Management, to other services like Outsourced Regulatory Affairs, Submissions, Training, and more.
As your partner, we can negotiate the potential assessment minefield of regulatory compliance services with insight, hindsight, and the clear advantage of our breadth and depth of knowledge and regulatory compliance consulting. We offer the following pharma consulting regulatory affairs services for pharmaceutical companies.
- New Product Support
- Product Lifecycle
- Other Regulatory Services
- Combination Products
The regulations process surrounding pharmaceutical companies can be tricky for even the most experienced industry veteran to understand. Just one misstep could mean significant and lasting consequences for your business. At Regulatory Compliance Associates, we offer the pharma consulting experience and pharma consultants necessary to guide you through the quality compliance process.
- Assessments
- Audits
- Regulatory Agency Response
- Preparation and Training
- Inspection Readiness
- Data Integrity
Regulatory Compliance Associates Quality consulting includes assessments, strategy, implementations, staff augmentations, and identification of quality metrics to ensure continuous improvement. Our pharma consultants understand the strategic thinking needed to align your business needs and goals. Regulatory Compliance Associates quality assurance services include quality experts with experience spanning major corporations and start-ups. Our pharmaceutical consulting firm knows firsthand how to achieve, maintain, and improve quality, and we excel in transferring pharma consulting knowledge to your organization.
- 21 CFR Part 11
- Data Integrity
- Manufacturing Support
- Facility Support
- Quality Metrics
Regulatory Compliance Associates has a proven remediation services approach to managing FDA Warning Letters, Consent Decrees, Remediation and other serious regulatory situations. Our pharma consultants know how to partner with executive, legal, and communication teams. Each RCA pharma consulting Expert will develop a response that will be accepted by the regulatory agency and be realistic to execute.
Regulatory Compliance Associates pharma regulatory consultants will develop a comprehensive proof book of documented evidence demonstrating the corrective action taken to remediate non-compliant issues. In addition, each Regulatory Compliance Associates pharma consulting Expert understands compliance enforcement. We’ll prepare a comprehensive pharma consulting strategy to assist in your remediation efforts, drive continuous improvement, and maintain regulatory compliance with the regulations.
- Regulatory Action
- Regulatory Compliance
- Regulatory Enforcement
- Warning Letter
- 483 Observation
- Oversight Services
- Risk Management Plan
About Regulatory Compliance Associates
Regulatory Compliance Associates® (RCA) provides pharmaceutical consulting to the following industries for resolution of life science challenges:
We understand the complexities of running a life science business and possess areas of expertise that include every facet of R&D, operations, regulatory affairs, quality, and manufacturing. We are used to working on the front lines and thriving in the scrutiny of FDA, Health Canada, MHRA and globally-regulated companies.
As your partners, we can negotiate the potential minefield of regulatory compliance and regulatory due diligence with insight, hindsight, and the clear advantage of our unique expertise and experience.
- Founded in 2000
- Headquartered in Wisconsin (USA)
- Expertise backed by over 500 industry subject matter experts
- Acquired by Sotera Health in 2021
About Sotera Health
The name Sotera Health was inspired by Soteria, the Greek goddess of safety, and reflects the Company’s unwavering commitment to its mission, Safeguarding Global Health®.
Sotera Health Company, along with its three best-in-class businesses – Sterigenics®, Nordion® and Nelson Labs®, is a leading global provider of mission-critical end-to-end sterilization solutions and lab testing and advisory services for the healthcare industry. With a combined tenure across our businesses of nearly 200 years and our industry-recognized scientific and technological expertise, we help to ensure the safety of over 190 million patients and healthcare practitioners around the world every year.
We are a trusted partner to 5,800+ customers in over 50 countries, including 40 of the top 50 medical device companies and 9 of the top 10 pharmaceutical companies.
Commitment to Quality
Our Certificate of Registration demonstrates that our Quality Management System meets the requirements of ISO 9001:2015, an internationally recognized standard of quality.
To begin the Regulatory Compliance Associates scoping process today, please enter your information in the blue form below and click the submit button at the bottom of the webpage.