Contract manufacturing organizations that manufacture traditional and biotech pharmaceutical products are responsible for performing investigations and reporting the results to their clients. But how do biologics consultants recognize the differences between performing an investigation of a biologic product versus pharmaceutical products?
Biologics Manufacturing
The short answer is there is no process difference when performing deviation investigations for traditional pharmaceutical products vs. biologic products. The differences lie in the complexity of the manufacturing processes. Further, these are the variables that should be considered regarding what could impacted the deviation.
Biotechnology Process
Chemical processes, although sometimes quite complex, often have fewer variables even though many of the categories are the same. For instance, when investigating an unknown impurity in a biological process from an oligopeptide fermentation process, the considerations are many. This often includes understanding the fermentation conditions, such as time, temperature, oxygen uptake and byproduct production.
Contamination
Moreover, potential contamination of reactants can include master cell banks and fermentation reagents, equipment integrity, and overall performance. Further considerations for the downstream purification process variables and the effect of a final configuration (e.g., folding) also need to be considered.
The purpose of a deviation investigation is to determine why the deviation happened and what its impact was on the product quality. To determine the impact of the deviation on biotechnology engineering in general, it is critically important to find the deviation root cause.
Root Cause Analysis
Conducting a root cause analysis is especially important when considering the COVID-19 pandemic and global impact on biological matrix supply chain. Small cap or start up biologics companies have virtually no room for production errors in this type of environment. For example, patients may be waiting for biologic medications and any production interruption can impact more than just the manufacturer.
The process used in the industry to determine root cause is, of course, the investigation procedure. This procedure, regardless of whether the product is biotech or traditional, should require the investigator to review various production systems. Equally important, the system review during the investigation should help determine whether they were the cause of the deviation under investigation.
Engineering Validation
Every biologics consultant understands it is important to remember when performing an investigation to keep in mind a few general rules. Naturally, one size does not fit all. Simple errors require simple corrections while serious deviations require broader investigations. Validating the investigation is related not only to the seriousness of the deviation but also to the complexity of the factors that could influence the outcome.
Fishbone Diagram
The best tool to have during any investigation is inquisitiveness. Continuing to ask questions and avoid assumptions will lead to a better outcome. Using other tools, such and fishbone diagrams and determination of most probable number (MPN), are always encouraged. Undeniably, they do not take the place of a biologics consultant asking questions.
Biologic Performance
In performing an investigation, it is important for the biologic investigator to widen their performance perspective and look for ways to relate similar issues. The best way to ensure events are not related is to try and relate them, not the other way around. Keep in mind that human error is rarely a true root cause. There is usually something in the process that causes that human error.
And finally, always verify the facts of the investigation. It is also important to include a historical review. This review should determine if the deviation occurred with this or other products, with the specific manufacturing line or other manufacturing lines, and/or with the operators.
Biopharma Tools
The historical review can help to prioritize the resources and detailed system review. In addition, many biopharma companies make use of tools (fishbone diagram, MPN) to help prioritize resources. These tools, if used correctly, can be helpful in determining root cause. However, keep in mind they are just tools and do not take the place of thinking.
The detailed investigation should include a review of various systems. The systems most often reviewed are equipment and machinery, the manufacturing process, the raw materials used in manufacturing, the specifications, the environment, and finally, the operators.
Finally, this is not to imply that these systems are the only areas you should look at during the investigation. These are simply the most probable areas where you will uncover the root cause of the deviation.
CAPA & Corrective Action
Each investigation must address the following elements: root cause, impact to the material or product, the immediate correction taken, the corrective action to prevent re-occurrence for specific product/operation, and the preventive action taken to prevent re-occurrence for all products/operations.
Once these elements have been investigated, results from the investigation must be documented. The written narrative should clearly explain what happened, when it happened, and who was involved or observed what happened. The narrative documents the solution and rationale for the root cause that was determined through the investigation process.
Quality Assurance
The key to any successful investigation is not assuming you have the solution prior to completing the investigation. Increase your quality assurance and compliance by asking questions until you can think of no more questions to ask. Be sure to document the answers to your questions.
If you follow your investigation procedure and thoroughly document your results, you should have an acceptable investigation regardless of whether you are manufacturing a traditional product or a biotech product.
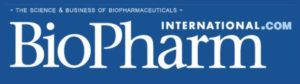
BioPharm International
Vol. 28, No. 11
Page: 46–47
About RCA’s Biotechnology Services
Regulatory Compliance Associates® Inc. can assist you in ensuring the quality of your biologics or biosimilar product during its entire lifecycle. From pre-market to post-market reviews, inspection, and compliance, our Biotech consulting experts can shepherd your biologics through design, labeling, promotion, production, and testing. Our Biologics services include:
Client Solutions
Whether you’re in the product planning, development or pharmaceutical lifecycle management stage or need a remediation strategy for a compliance crisis, Regulatory Compliance Associates will guide you through every pharmaceutical consulting step of the regulatory process and create a customized approach depending on your product and your pharma company’s individual needs. Our regulatory compliance clients include:
- Companies new to FDA, Health Canada or EU regulations and regulatory compliance
- Start-up organizations with novel submissions to 510(k) submissions from multi-national corporations
- Investment firms seeking private equity due diligence for pre-acquisition and post-deal research
- Law firms seeking pharmaceutical consulting firm expertise in the remediation of warning letters, consent decrees, 483’s or import bans
Regulatory affairs is Regulatory Compliance Associates backbone. We exceed other pharma consulting companies with industry experts experienced in complexities of the pharmaceutical and biopharmaceutical industries. Our pharma consulting expertise spans all facets and levels of Regulatory Affairs, from Regulatory Support for New Products to Life Cycle Management, to other services like Outsourced Regulatory Affairs, Submissions, Training, and more.
As your partner, we can negotiate the potential assessment minefield of regulatory compliance services with insight, hindsight, and the clear advantage of our breadth and depth of knowledge and regulatory compliance consulting. We offer the following pharma consulting regulatory affairs services for pharmaceutical companies.
- New Product Support
- Product Lifecycle
- Other Regulatory Services
- Combination Products
The regulations process surrounding pharmaceutical companies can be tricky for even the most experienced industry veteran to understand. Just one misstep could mean significant and lasting consequences for your business. At Regulatory Compliance Associates, we offer the pharma consulting experience and pharma consultants necessary to guide you through the quality compliance process.
- Assessments
- Audits
- Regulatory Agency Response
- Preparation and Training
- Inspection Readiness
- Data Integrity
Regulatory Compliance Associates Quality consulting includes assessments, strategy, implementations, staff augmentations, and identification of quality metrics to ensure continuous improvement. Our pharma consultants understand the strategic thinking needed to align your business needs and goals. Regulatory Compliance Associates quality assurance services include quality experts with experience spanning major corporations and start-ups. Our pharmaceutical consulting firm knows firsthand how to achieve, maintain, and improve quality, and we excel in transferring pharma consulting knowledge to your organization.
- 21 CFR Part 11
- Data Integrity
- Manufacturing Support
- Facility Support
- Quality Metrics
Regulatory Compliance Associates has a proven remediation services approach to managing FDA Warning Letters, Consent Decrees, Remediation and other serious regulatory situations. Our pharma consultants know how to partner with executive, legal, and communication teams. Each RCA pharma consulting Expert will develop a response that will be accepted by the regulatory agency and be realistic to execute.
Regulatory Compliance Associates pharma regulatory consultants will develop a comprehensive proof book of documented evidence demonstrating the corrective action taken to remediate non-compliant issues. In addition, each Regulatory Compliance Associates pharma consulting Expert understands compliance enforcement. We’ll prepare a comprehensive pharma consulting strategy to assist in your remediation efforts, drive continuous improvement, and maintain regulatory compliance with the regulations.
- Regulatory Action
- Regulatory Compliance
- Regulatory Enforcement
- Warning Letter
- 483 Observation
- Oversight Services
- Risk Management Plan
About Regulatory Compliance Associates
Regulatory Compliance Associates® (RCA) provides pharmaceutical consulting to the following industries for resolution of life science challenges:
We understand the complexities of running a life science business and possess areas of expertise that include every facet of R&D, operations, regulatory affairs, quality, and manufacturing. We are used to working on the front lines and thriving in the scrutiny of FDA, Health Canada, MHRA and globally-regulated companies.
As your partners, we can negotiate the potential minefield of regulatory compliance and regulatory due diligence with insight, hindsight, and the clear advantage of our unique expertise and experience.
- Founded in 2000
- Headquartered in Wisconsin (USA)
- Expertise backed by over 500 industry subject matter experts
- Acquired by Sotera Health in 2021
About Sotera Health
The name Sotera Health was inspired by Soteria, the Greek goddess of safety, and reflects the Company’s unwavering commitment to its mission, Safeguarding Global Health®.
Sotera Health Company, along with its three best-in-class businesses – Sterigenics®, Nordion® and Nelson Labs®, is a leading global provider of mission-critical end-to-end sterilization solutions and lab testing and advisory services for the healthcare industry. With a combined tenure across our businesses of nearly 200 years and our industry-recognized scientific and technological expertise, we help to ensure the safety of over 190 million patients and healthcare practitioners around the world every year.
We are a trusted partner to 5,800+ customers in over 50 countries, including 40 of the top 50 medical device companies and 9 of the top 10 pharmaceutical companies.
Commitment to Quality
Our Certificate of Registration demonstrates that our Quality Management System meets the requirements of ISO 9001:2015, an internationally recognized standard of quality.
To begin the Regulatory Compliance Associates scoping process today, please enter your information in the blue form below and click the submit button at the bottom of the webpage.