Medical Devices
When a medical product fails in the field, everyone suffers — not just the patient, but also the manufacturer and its employees, investors, suppliers, and even competitors. No one wants a product failure, least of all the liable company for its safety. Faced with a quality investigation crisis, the manufacturer has three priorities: (1) protect patients; (2) resolve the problem as quickly as possible; and (3) prevent the problem from recurring.
Any product failure threatens a huge loss of value, above and beyond liability, to the manufacturer. If investors lose confidence and share price falls, enterprise value is destroyed. Then, as the company dedicates resources to resolving the problem, their other jobs — such as new product development — don’t get done (or, at best, don’t get done as quickly).
Risk Management
Since innovation is the beating heart of the medical device industry, any delay of a new product launch can cost a manufacturer millions; time really is money. All the more reason that quality investigation speed is so important in fixing any product problem.
Yet, many companies are not really prepared for product failure because they lack a crisis playbook. Through our work in helping companies investigate and resolve product failures, Regulatory Compliance Associates and The Science Cooperative (Chicago, IL) have gained the following insights about what works (and what doesn’t) in managing a product crisis.
“First Responders”
A problem is identified as serious when field events indicate a trend beyond isolated incidences. At that time, the company’s leadership has to make a few decisions: Should an official notice be released? Should the product be recalled? Everywhere or only in some markets? Should production be stopped? In multiple or select plants?
Prompt action generally contributes to good will and positive publicity during a quality investigation. But the challenge is a deficit of facts at this stage since the forensic investigation itself hasn’t started.\
Standard Operating Procedure
In putting together a crisis playbook, a company should begin with guidelines and policies to direct the first responders in evaluating the size of the threat and the appropriateness of various options for response, depending on the apparent scope and severity of the problem.
For example, if a product is one component in an assembly, perhaps the best response is for multiple supply chain owners to work together to find the optimal fix for the problem. Among other issues that could be decided in advance would be choosing the “point man” for making that happen.
Risk Assessment
Of course, a crisis playbook would also help business leaders evaluate the cost of alternative responses. Say the chance of the company’s product being the cause of the crisis is 20 percent and pulling it off the market would cost $500 million: what’s the optimal strategy for moving forward?
Scenario-based planning provides a context for weighing alternatives and options during a quality investigation. But above all else, the first responders would want to stop patient harm; protecting the safety of the patient population comes first.
Functional Forensic Teams: Divide & Conquer
After the first responders have reviewed the situation and decided there is cause for escalation, it’s time to identify an investigation leader/crisis manager, an investigation leader, and the functional forensic team(s). An attorney or senior executive with strong project management skills is a good choice for crisis manager; also, each team needs at least one a member with strong organizational skills.
Product Validation
The crisis playbook should cover roles and responsibilities — including potential action checklists — for multiple functional forensic teams across the quality investigation. It’s feasible that a crisis might require teams in R&D, sciences, manufacturing, distribution, supply chain, human resources, legal, regulatory, quality, environmental, sales/marketing, and communications, as well as sub-teams for representatives from affected countries and from government affairs.
What expertise would each team require? What would be each team’s scope and focus? Most important, how should the teams interact, coordinate activities, and measure progress toward milestones and a final resolution? A crisis playbook should provide answers, which would vary case by case.
Project Management
Good project management skills are fundamental to managing the investigation process effectively and efficiently. Although the teams are all working on the same problem, each requires its own plan and milestones.
Role-based accountability for project and team-specific organization, documentation, schedules, data management, and reporting can be decided well in advance of a crisis. It’s best that the leaders of the crisis management team meet daily to assure clear, timely, cross-functional communication and to agree on next steps.
Resources: Knowledge & “Know-How”
If valuable resources are taken away or distracted from their jobs to any significant degree, real and measurable enterprise value is destroyed. So, while leaders and experts from each affected corporate function play a vital role in an investigation, it may be a smart business strategy to bring in specialists to support the effort with their expertise and experience.
In addition to minimizing damage to the company’s value and brand, the quick building up of expertise also speeds up the forensic process itself. One client asked both the FDA and EU notified bodies to participate in an investigation; as a result, the company tripled its lab capacity and bolstered credibility with shareholders and the marketplace.
FDA Investigation
Independent consultants can add muscle to any FDA investigation, while buttressing investor confidence. As an added benefit, because they’re beyond the “politics” of the enterprise, they can often give employees the freedom to speak without repercussion. Also, outside resources with the right knowledge and “know-how” will be well versed in Corrective and Preventive Action (CAPA) processes and can use this expertise to streamline and speed up the investigation.
Roadmap: Imagine a Practical Path Forward
Each team needs a directed course of action based on scenario planning. Given a set of variables that would vary by product and case — including (but not limited to) the severity of the crisis, geography, financial liability, and the possibility of substitute products — what steps should each team take to contribute to the problem identification, resolution, and ongoing prevention?
The steps required of each team can be captured in “punch lists” to minimize redundancy and duplication of effort. Then, it’s relatively easy to assign responsibility for each item on the list. If the product is used in more than one country or region, the work of the corporate teams needs to be mirrored by local teams, and everyone’s findings need to roll up to the top.
Root Cause Analysis
Perhaps one of the most critical points in the quality investigation roadmap — and the one that’s most often missing — is a “stop” point. The longer an investigation goes on, the more enterprise value it can destroy.
So, in the beginning, it is important to decide: When is the problem solved? Is it when the contaminant is found? When the process in the factory or the supply chain is fixed? Or when the product is reintroduced to the market? Among these inquiries is another with implications for continuous improvement: Why didn’t the QA processes in place (for design, manufacturing, and other functions) detect the potential failure?
Scope control is a fundamental component of good project management. In most cases, there’s no need to parse the problem beyond a practical solution. The crisis playbook should include prototype action plans, checklists, work streams, decision processes, schedules, milestones, resource requirements, budgets, and documentation.
Steps for Post-Crisis Resolution:
- Assure that all commitments made have been honored.
- Update all prevention measures, including software procedures and policies, as appropriate.
- Debrief the crisis management teams to mine “lessons learned”.
- Ensure appropriate closure communication with key stakeholders, including regulatory agencies, media, customers, investment community, and employees.
Strategic Communication
From day one, the investigation leader/crisis manager needs to share information about commitments, expectations, and progress. Communication — internally with employees and externally with investors, supply chain partners, regulatory agencies, the public, and sometimes competitors — is critically important.
The overall process needs a “point person” for communication, as does each team, whether at the corporate or local level. The role of each communication channel — including press releases, internal newsletters or briefs, media contacts, video, and letters to shareholders and the investment community — can be planned well in advance: a crisis playbook can take chaos out of the process and enable the company to put its best foot forward. In communication, the current best practice is a dedicated portal, a single source for real-time updates on the investigation, typically accessible through the company’s Website.
Crisis Management
The old proverb “a stitch in time saves nine” captures the value of a crisis playbook: being prepared will save time and money down the road; most importantly, it could literally save lives. By being mindful of the components of effective and efficient crisis management — building up and deploying expert resources; coordinating and integrating parallel work streams; following and documenting rationalized processes — a company’s leadership can be confident in its preparedness to handle a product failure to the satisfaction of everyone’s best interests.
Article Details
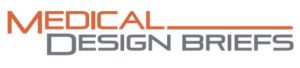
Complete article published in Medical Design Briefs.
About RCA’s Medical Device Consulting Services
The regulatory compliance process surrounding the medical device industry involves a strict adherence to pre/post market information throughout a device’s life-cycle. Even a single compliance issue you have can turn into a significant effect on your business. Regulatory Compliance Associates medical device consultants can help guide you through any stage of this strategic process, with capabilities during product development through the regulatory clearance/approval of your product.
Our team of over 500 medical device consulting Experts — including former FDA officials and regulatory compliance leaders in the field of medical device regulation — will work with your company to create a quality assurance and regulatory compliance approach tailored to your products and regulatory needs. Regulatory Compliance Associates works with international Fortune 100 companies, venture capital start ups, and companies of all sizes and shapes. our compliance enforcement solutions for law firms include remediation for warning letters, FDA 483’s, import bans or consent decrees. Very few regulatory compliance services have the same regulatory compliance expertise in a variety of medical fields.
For medical device manufacturers, technology can be a double-edged sword. The innovative technologies that elevate the quality of life for patients can also be used to potentially undermine the organization using the device. The consequences can affect the device itself if Regulatory Compliance Associates medtech consultants do not implement good IoT cybersecurity and FDA cybersecurity protocols.
At Regulatory Compliance Associates, we offer a wide variety of services for medical devices security to help ensure that your product is protected from cyber-attacks. With a well-planned design, along with full visibility of product development and the supply chain, Regulatory Compliance Associates medical device consultant Experts can help strengthen your device’s cybersecurity. We partner with medical device companies in each phase of the design cycle, including protecting inputs from threat exposure and hardening outputs for regulatory compliance & FDA submission approval of your medical technology.
Regulatory affairs is Regulatory Compliance Associates® backbone, and we handle more submissions in a month than many manufacturers do in a lifetime. Our regulatory compliance consulting Experts have experience working with the FDA, global regulatory bodies and / or agencies, and notified bodies worldwide. Therefore, you can count on us for in-depth and up-to-date insights which increase speed-to-market.
As a trusted regulatory affairs consultant, our FDA veterans and industry experts represent Regulatory Compliance Associates® as one of the top medical device consulting firms. We’re here to help you navigate the difficulties associated with new product submissions. Regulatory Compliance Associates® medical device consulting company has expertise in both the approval process and post-approval support.
- New Product Approval
- Post-Approval Support
- Outsourced Staffing
- EU MDR
- Combination Products
Increasingly, life science companies are feeling the pressure of greater scrutiny by regulators, and responding by developing sustainable compliance strategies. Whether it’s preparing for an audit, developing a response to an FDA finding, or remediation to an adverse event, Regulatory Compliance Associates® can help.
Our network of over 500 medical device consultant & FDA, MHRA & EMA veterans are industry professionals offers a unique blend of expertise. This allows Regulatory Compliance Associates® to handle both simple and complex regulatory compliance challenges within medical device consulting companies.
- Gap Assessments
- Internal Audits
- Employee Training
- Notified Body Response
- Data Integrity
Regulatory Compliance Associates® Quality Assurance consulting includes quality system assessments, strategy, implementations, and identification of quality metrics to ensure continuous improvement, aligning with your business needs and goals. Each Regulatory Compliance Associates® medical device consultant is a quality expert with experience spanning major corporations and start-ups. We know firsthand how to achieve, maintain, and improve quality, and we excel in transferring this knowledge to your organization.
In the medical devices field, quality assurance (QA) is more than merely ensuring the quality of a finished product. You need the tools to monitor and regulate every process from the design of a new product to continued quality compliance as the device is sent to market. At Regulatory Compliance Associates®, we offer you the quality assurance services you need to monitor these processes and ensure quality compliance every step of the way.
With more than 20 years experience working with medical device consulting companies, Regulatory Compliance Associates® trusted medical device quality assurance consultant team is fully equipped to handle your unique QA needs.
- ISO13485
- 21 CFR 210
- 21 CFR 211
- Outsourced Staffing
- MDSAP
- Facility Validation
- Equipment Validation
- Quality Metrics
Regulatory Compliance Associates® is widely recognized within medical device consulting companies & the life science industry for remediation support. Regulatory Compliance Associates® ability to help companies successfully resolve complex regulatory challenges have a proven track record of success. Our medical device consulting services include significant experience with the development of responses to 483 Observations, Warning Letters, Untitled Letters and Consent Decrees.
- Regulatory Action
- Regulatory Compliance
- Regulatory Enforcement
- Warning Letter
- 483 Observation
- Oversight Services
Our value goes beyond the initial response by helping companies successfully execute their action plans, develop an improved compliance culture tailored to the needs of their business, and ultimately move beyond the regulatory action to emerge as a stronger business. We negotiate difficult demands of remediation with insight and the clear advantage of our medical device consultant expertise and experience that makes partnering with Regulatory Compliance Associates® a competitive differentiator in the remediation space.
- Quality System
- Technical File
- Design History File
- Data Integrity
- cGMP
Whether it’s a strategy, a technical plan, or project, Regulatory Compliance Associates® medical device consultancy can help ensure a successful project. Regulatory Compliance Associates® medical device strategy consulting can deliver your project on time, on budget, and you’re never embroiled in a costly mistake.
Our medical device consultant Experts are industry Experts are here to provide the unique insight you need before an M&A deal, through a staffing crisis and in every area of your product’s development and life cycle. As the trusted medical device manufacturing consultants of thousands of companies around the world, we have the knowledge and expertise needed to deliver exceptional results to your business — no matter your size or unique needs.
- Manufacturing Optimization
- Product Lifecycle Management
- Mergers & Acquisitions (M&A)
- Due Diligence
- Device Vigilance
- Risk Management Plan
- Product Complaints
- Medical Information
About Regulatory Compliance Associates
Regulatory Compliance Associates® (RCA) provides medical device consulting to the following industries for resolution of life science challenges:
We understand the complexities of running a life science business and possess areas of expertise that include every facet of R&D, operations, regulatory affairs, quality, and manufacturing. We are used to working on the front lines and thriving in the scrutiny of FDA, Health Canada, MHRA and globally-regulated companies.
As your partners, we can negotiate the potential minefield of regulatory compliance and regulatory due diligence with insight, hindsight, and the clear advantage of our unique expertise and experience.
- Founded in 2000
- Headquartered in Wisconsin (USA)
- Expertise backed by over 500 industry subject matter experts
- Acquired by Sotera Health in 2021
About Sotera Health
The name Sotera Health was inspired by Soteria, the Greek goddess of safety, and reflects the Company’s unwavering commitment to its mission, Safeguarding Global Health®.
Sotera Health Company, along with its three best-in-class businesses – Sterigenics®, Nordion® and Nelson Labs®, is a leading global provider of mission-critical end-to-end sterilization solutions and lab testing and advisory services for the healthcare industry. With a combined tenure across our businesses of nearly 200 years and our industry-recognized scientific and technological expertise, we help to ensure the safety of over 190 million patients and healthcare practitioners around the world every year.
We are a trusted partner to more than 5,800 customers in over 50 countries, including 40 of the top 50 medical device companies and 8 of the top 10 pharmaceutical companies.
Commitment to Quality
Our Certificate of Registration demonstrates that our Quality Management System meets the requirements of ISO 9001:2015, an internationally recognized standard of quality.
To begin the Regulatory Compliance Associates® scoping process today, please enter your information in the blue form below and click the submit button at the bottom of the webpage.