Case Studies
Medical Device Validation: Shelf Stability
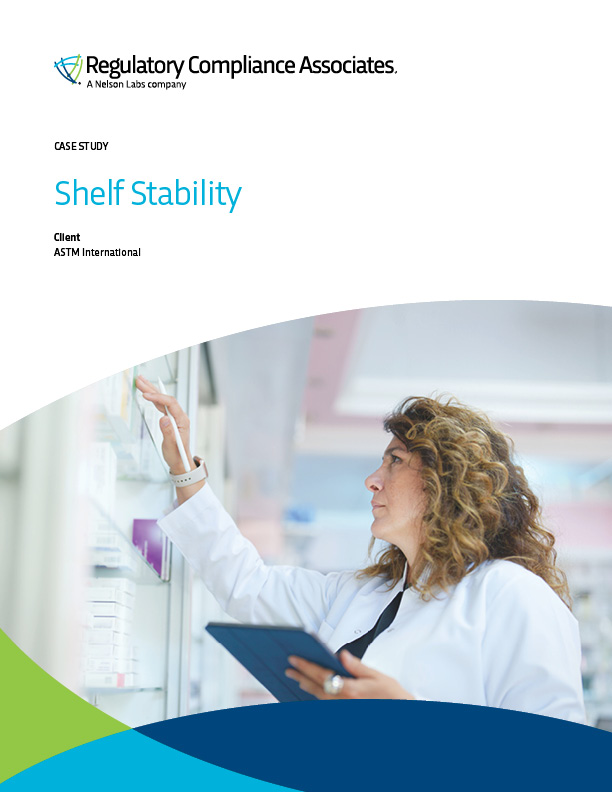
Client
ASTM International
Industry
Medical Device
Business Challenge
Create a new design for a product to ensure a successful launch
Background
A large medical products manufacturer encountered a critical issue during the development of a new blood collection device. Accelerated shelf-age validation testing revealed that the protective sheath surrounding the needle did not maintain adequate reseal integrity after aging. Post-aging, the sheath failed to reliably prevent blood leakage following needle puncture—a problem not observed in unaged test samples. These unexpected reseal failures delayed the development timeline and posed a significant risk to the overall success of the product launch.
RCA Approach
Regulatory Compliance Associates® Inc. (RCA) was brought in to investigate the root cause and identify a viable material solution. The original sheath material was synthetic polyisoprene. RCA led a series of experiments evaluating alternative synthetic polyisoprene formulations. However, it was ultimately determined that meeting the required reseal performance would necessitate transitioning to natural polyisoprene (natural rubber latex), known for its superior elasticity and resealing capabilities.
Result
Following the material change, the device successfully passed design verification and validation testing. Subsequent design reviews and design transfer activities were completed, the design history file was updated, and the product was successfully launched using natural rubber latex sleeves.