Case Studies
Production and Process Control
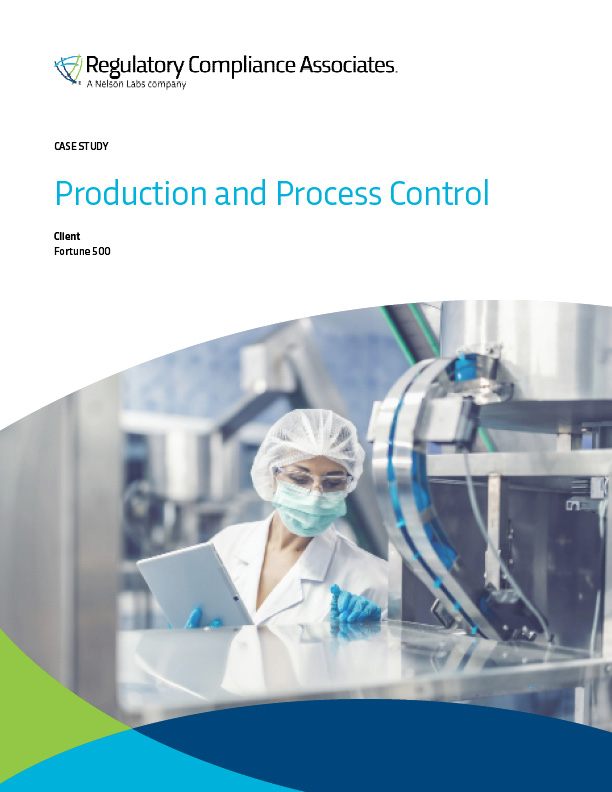
Client
Major Pharmaceutical Company
Industry
Pharmaceutical
Business Challenge
Remediation of a FDA 483 across multiple manufacturing sites
Background
A Fortune 500 biotechnology company faced ongoing challenges during campaign changeovers due to missing parts critical to equipment assembly. These deficiencies frequently led to costly, last-minute part fabrication and heightened the risk of production delays and revenue loss. Each near-miss placed increasing stress on operations management and threatened overall manufacturing continuity.
Further complicating the issue, equipment setup was based solely on Process and Instrumentation Diagrams (P&IDs) and relied heavily on employee memory, making the process inconsistent and prone to human error.
Regulatory Compliance Associates® Inc. (RCA) was engaged to identify and implement a comprehensive solution. During the initial assessment, RCA determined that the existing process lacked proper documentation and did not meet current Good Manufacturing Practice (cGMP) requirements. The solution not only needed to resolve the missing parts issue, but also establish robust GMP-compliant documentation to ensure the process was repeatable, controlled, and inspection-ready.
RCA Approach
Following a thorough investigation, RCA developed and implemented a standardized process to eliminate the recurring issues. This solution included the creation of detailed build lists, standard operating procedures (SOPs) featuring embedded color photographs, and 3D exploded diagrams for each equipment setup. To improve traceability and ease of identification, all equipment components were laser-etched with part numbers aligned with the supporting documentation. Campaign-specific sealed containers were introduced to organize and secure the necessary parts in advance of changeovers. RCA also conducted extensive employee training and established continuous improvement metrics to monitor performance and ensure long-term program sustainability.
Result
As a result of RCA’s solution, missing parts during equipment setup have been fully eliminated. The new documentation meets cGMP requirements and now serves as a key training resource, significantly reducing reliance on tribal knowledge. Campaign changeover times have been reduced by a minimum of two days—and up to six days in some cases—leading to a substantial annual cost savings of $4 million.