Case Studies
Improved Product Release Cycle Times, Improved Bottom Line
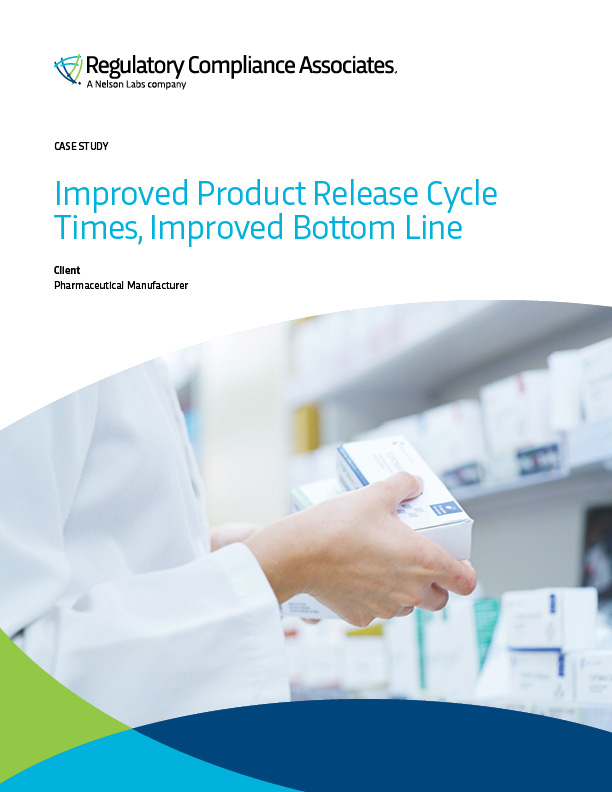
Client
Pharmaceutical Manufacture
Industry
Pharmaceutical
Business Challenge
To improve the efficiency during manufacturing
Background
A generic pharmaceutical manufacturer was interested in applying lean principles to the operation of the Quality team, with the objective to reduce the product release time frame. However, they lacked internal experience to embark upon this initiative.
The client engaged RCA’s experts to enhance operational efficiency across manufacturing processes, streamline batch record review, and accelerate product release to the distribution network.
RCA Approach
RCA’s experts employed process mapping to uncover redundancies, inefficiencies, and key areas for improvement. Collaborating closely with company process owners, they systematically designed and implemented optimized workflows across both Quality and Manufacturing operations.
Result
RCA experts successfully streamlined the product release process from 30 days to just four. This significant reduction in cycle time minimized the need to hold costly unreleased inventory, enabling the company to decrease its inventory investment while enhancing the speed and reliability of product delivery. Implemented across multiple manufacturing sites, this improvement had a substantial impact on cash flow—estimated by internal experts to be $50 million.*
Accelerating the movement of work-in-progress inventory into finished goods allowed the company to reduce carrying costs and optimize floor space utilization. The shortened product release cycle also led to fewer back orders and minimized short-dating issues. Furthermore, for certain export markets, the improved timeline enabled the company to shift from costly air freight to more economical sea freight, further reducing distribution expenses.
*Cash Flow Improvement = product unit cost X # units produced/day X # days release cycle time improvement