Case Studies
Pharmaceutical Shipping Validation Study
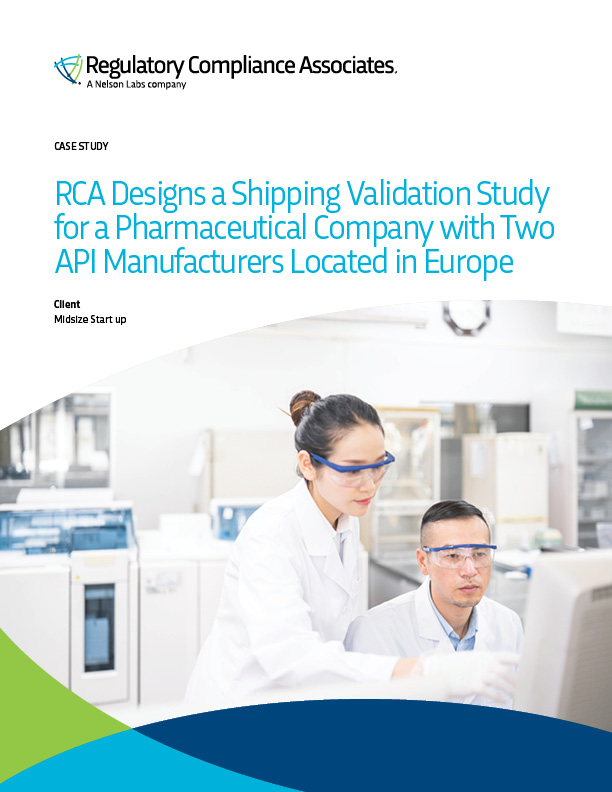
Client
Mid-size start up
Industry
Pharmaceutical
Business Challenge
Design a Pharmaceutical Validation Study that proves the SQUIPP of the drug product is maintained throughout the multinational manufacturing and distribution process given the multiple modes of transportation.
Background
A pharmaceutical start-up, located in the USA, approached RCA to design their shipping validation study given the complexity of their supply chain, manufacturing, and distribution process.
The challenge is to design a study that proves the SQuIPP of the drug product is maintained throughout the multi-national manufacturing and distribution process given the multiple modes of transportation and multiple hand offs between four different companies. The company has two API manufacturers, located in different parts of Europe, that they need qualified using both air and sea transportation between Europe and Canada. The finished drug product is to be manufactured in Canada and then shipped to the USA by air or ground transportation for distribution.
RCA Approach
Based on the request of the client, multiple shipping studies were required. Each API manufacturer needs to be qualified for each route using different modes of transportation, and each route needs to be challenged by “anticipated extremes”. There were a multitude of shipping configurations (# of drums, drum sizes, drum weights, # of pallets per container, types of containers, etc.) that differed by manufacturer, but in some cases also changed within the same manufacturer, that added complexity to this project. Additionally, any possible new challenges associated with international shipping practices had to be identified (languages, time zones, holidays, etc.).
RCA was able to generate multiple shipping study protocols. These protocols included representative transportation load configurations, defined packaging configurations, and calibrated temperature monitor positioning. Given the delicate nature of the API, lot samples were pulled and sent with each shipment to undergo chemical testing following shipment. The testing results were used to illustrate that the SQuIPP of the API material was not impacted by the shipment. Since the client couldn’t be present at each CSP site, the protocol included clear, multilingual instructions and diagrams to ensure correct temperature monitor placement and pallet configuration.
Multiple different companies were involved in manufacturing and distributing the finished product, therefore, the hand offs had to be effectively managed. Each company was required to provide documentation to RCA illustrating the protocol had been followed. Given that the product is temperature-sensitive, a delayed or missed hand off puts the product at risk. It was RCA’s job to analyze the shipment documentation and temperature data to determine whether the validation passes and generate the final reports.
Results
The company was able to provide sufficient data proving the drug product and it’s materials was maintained within the established temperature range throughout the cold chain distribution by all modes of transport during both winter and summer seasons. The data also illustrated the SQuIPP of the product was not impacted during the shipments. The thorough design of the study, combined with data tracking and analysis from RCA, enabled the company to prove this consistency over time.