Case Studies
Outsourced QA Leadership Benefits Emerging Device Maker
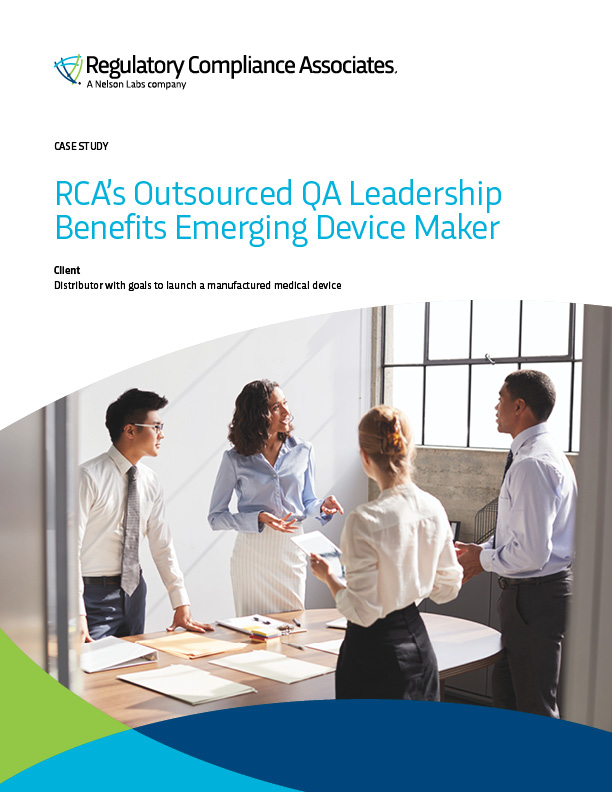
Client
Distributor with quality assurance goals to launch a manufactured medical device
Industry
Medical Device
Business Challenge
Set-up and management oversight of QMS for emerging device maker with financial constraints
Client Challenge
The client’s team had developed a strong business plan, secured a solid intellectual property (IP) platform, and established a clear manufacturing strategy. However, they lacked a defined regulatory affairs (RA) and quality pathway. Operating in a bootstrapped environment, they initially implemented off-the-shelf quality management system (QMS) software, only to later discover that this approach was insufficient to meet their regulatory and quality compliance needs.
RCA Approach
Regulatory Compliance Associates® Inc. (RCA) was engaged to perform a gap analysis, identifying discrepancies between the company’s existing systems and the regulatory affairs (RA) and quality management system (QMS) requirements. RCA initiated a structured remediation effort, providing targeted support where needed—such as aligning standard operating procedures (SOPs) with the company’s unique business needs and refining the product development process to meet evolving QMS expectations. To support the development of a compliant and robust QMS, RCA deployed experts in quality systems and quality engineering, including specialists in electronics.
As the new product launch approached, RCA further supported the implementation of a Corrective and Preventive Action (CAPA) system, a complaint management process, and an internal audit plan—ensuring a sustainable and inspection-ready quality infrastructure.
Results
Through the combination of RCA’s outsourced quality and regulatory expertise and the client’s internal team, the company successfully launched its product, achieved full regulatory compliance, passed audits, and implemented a robust Quality Management System—all without the need to hire costly full-time executives. By addressing compliance gaps and optimizing the use of existing QMS software, RCA helped the company preserve its prior investment and avoid unnecessary system replacement costs.
Additionally, RCA structured a flexible payment plan with fixed monthly fees, enabling the client to manage cash flow effectively during a critical growth phase. Following RCA’s initial engagement, the product achieved commercial success. As the company scaled, RCA was retained for ongoing support as the outsourced QA/RA manager, providing strategic guidance while keeping operational expenses manageable.
This successful partnership and the company’s continued growth ultimately attracted investor interest, culminating in an acquisition by one of the top 100 global medical technology companies.