Case Studies
FDA Warning Letter Response and Remediation
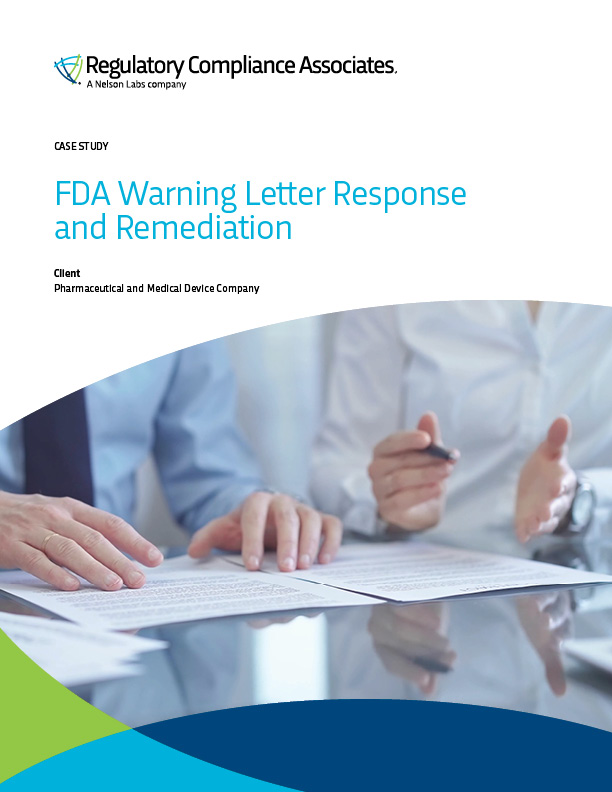
Client
Combination Products Manufacture
Industry
Pharmaceutical, Medical Device
Business Challenge
Developing a phased program plan that addresses FDA warning letters
Project Timeline
6 Months
Background
A mid-sized company received a 10-item FDA Form 483 and submitted an initial response. However, the response was followed by the issuance of a Warning Letter, leaving the company uncertain about how to effectively engage with the FDA moving forward. The agency had clearly outlined its expectations for the manufacturing of drug and device products at the site, and the management team—having already responded once—was unsure how to construct an appropriate and effective second response.
RCA Approach
Regulatory Compliance Associates® Inc. (RCA) developed a phased program to address both the FDA Warning Letter and broader quality system deficiencies. In Phase I, RCA delivered a detailed response to the Warning Letter, including aggressive timelines and objective evidence demonstrating completed corrective actions. Phase II focused on a comprehensive assessment and remediation of the overall quality system.
RCA created a detailed implementation plan featuring realistic yet ambitious milestones, clearly defined roles and responsibilities, and interdependent task structures to ensure accountability. To lead the initiative, RCA assigned a certified Project Management Professional (PMP), supported by engineers with deep expertise in quality systems and manufacturing engineering, who worked collaboratively with the client’s internal team to drive execution.
Result
The FDA received the Warning Letter responses, timelines, and supporting objective evidence favorably, leading to closure of the Warning Letter within just six months. The best-in-class project management practices applied during Phase II played a critical role in the successful, on-time, and on-budget achievement of key quality system compliance milestones.