Regulatory Compliance Associates (RCA) has helped thousands of pharmaceutical companies meet regulatory, compliance, quality assurance, and remediation challenges. With more than 20 years of experience with FDA, Health Canada, EU and global regulatory agencies worldwide,
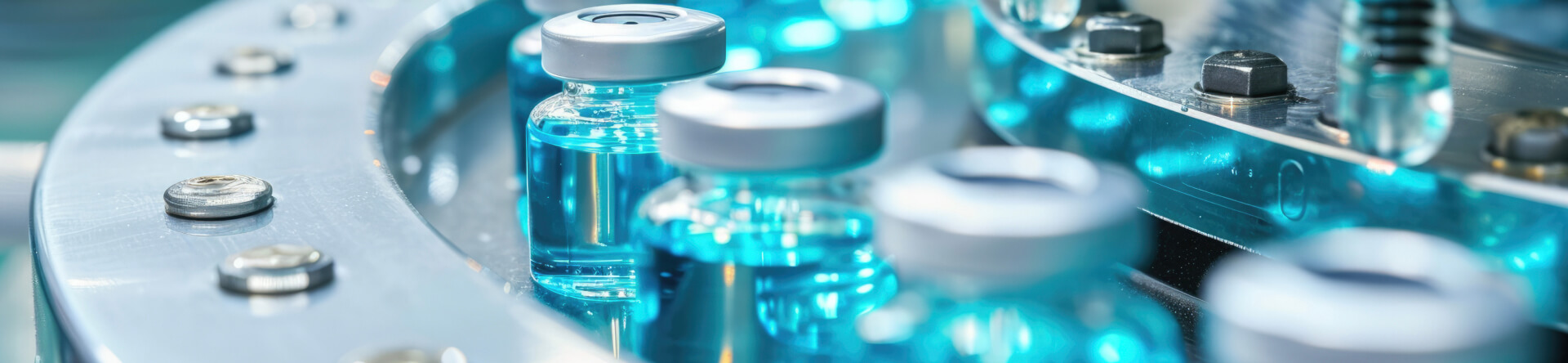
Pharmaceutical Consulting Services
Our team consists of a blend of both ex-FDA as well as industry experts who understand industry complexities. We have helped thousands of companies meet the ever changing compliance requirements.
Compliance Assurance
Regulatory Affairs
Quality Assurance
Remediation Services
Strategic Consulting
Connect with RCA Today
Contact us to learn more about our regulatory compliance experts and how they can help
